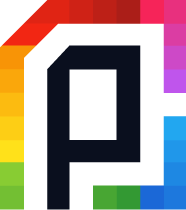
Claims Pages is unable to verify the information listed for "Metropolitan Corp" above. However, we can confirm that the business listings below are up-to-date and the providers are able to handle insurance claims work across the same set of locations and categories.